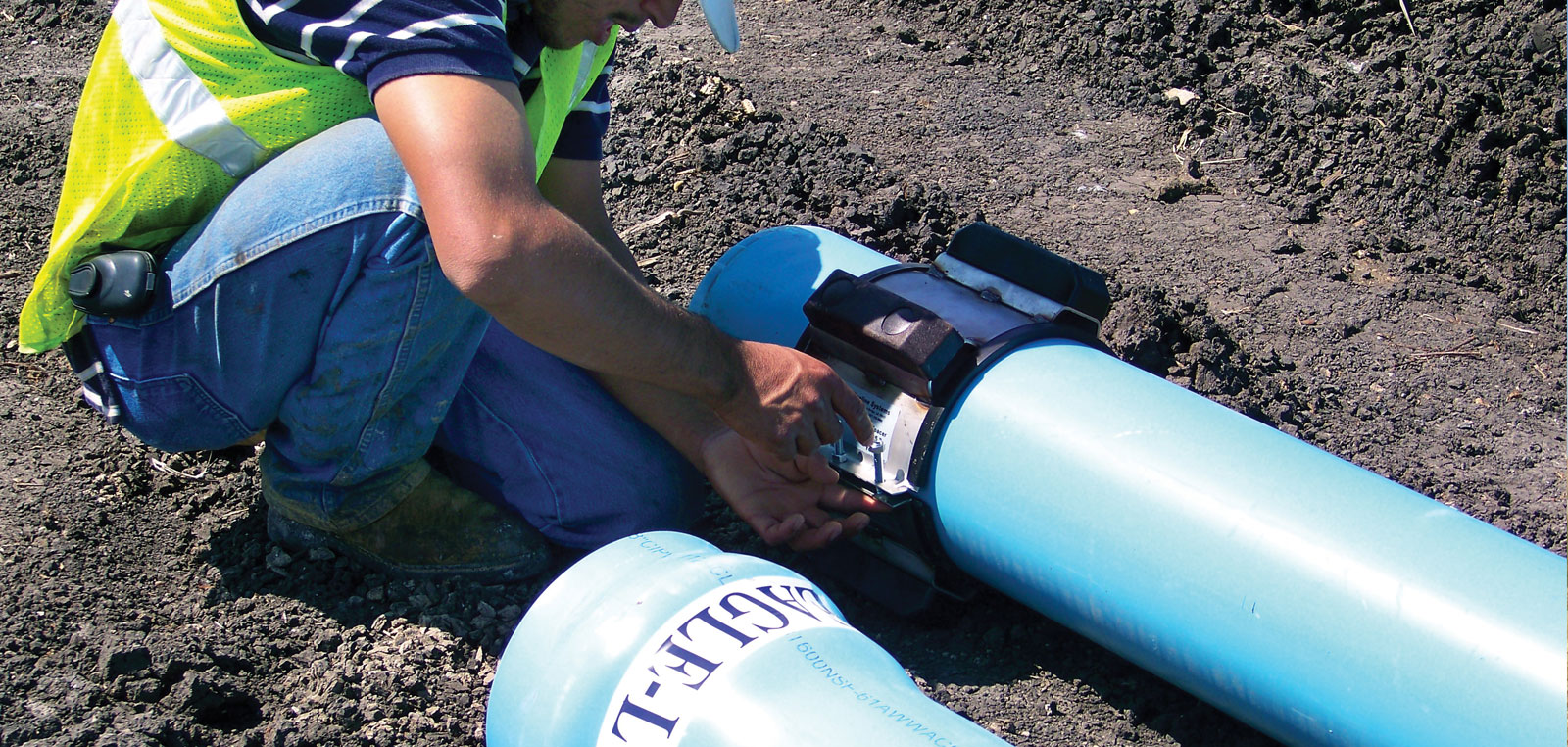
JM Eagle’s $350 Million Capital Investment is Increased by Another $20 Million
Decision made after three-year federal investigation of JM Eagle’s products and processes.
Los Angeles - March 24, 2010 — JM Eagle™, the world’s largest plastic-pipe manufacturer, today announced that it will invest an additional $20 million in 2010 to improve its manufacturing facilities as part of its Capital Improvement Project. Through its Capital Improvement Project, JM Eagle has invested more than $350 million over the past 15 years to employ the most modern manufacturing practices available to ensure its products set the standard for superior quality in the plastic-pipe industry. JM Eagle’s $20 million investment stands out in the plastic-pipe industry, where investments in facilities improvements and modernization investment has stalled over the past two years due to the recession.
“Our modernization projects are very important to us,” says JM Eagle Vice President of Operations Dave Slawson. “By using the most advanced technologies we make certain our products are of the highest quality and far exceed industry norms.”
JM Eagle’s additional $20 million investment will continue the advancements that allow the Company to produce the highest quality PVC pipe on the market and introduce new and innovative products in what is generally considered a commodity market. Specifically, it will continue to fuel the pace of the Company’s research and development to introduce the most innovative new products on the market, and improve automation and investments in high-end manufacturing equipment, the highest quality machines, state-of-the-art operating procedures, and rigorous routine maintenance.
JM Eagle purchases top-of-the-line polyvinyl chloride and polyethylene pipe extruders; these machines are equipped with ultra-modern automation systems; after installation, each extruder is outfitted with special tools that give plant managers the ability to monitor critical aspects of production, including extrusion speed, temperature and compound mixture levels; going a step further, these data are sent electronically to JM Eagle’s headquarters for assurance of quality.
“JM Eagle, as with all processors, [has] many choices when they select machinery vendors” says American Maplan Corp. President and CEO Kurt Waldhauer. “JM Eagle has chosen to purchase leading extrusion technology instead of significantly lower cost extrusion equipment that is typically iterations behind the technology curve.”
JM Eagle’s commitment to the latest technology has resulted in the Company’s introduction of two important new innovations to its product line. The first is the Eagle Loc 900™, a revolutionary internal joint restraint system that virtually eliminates the need for external joint restraints on PVC pipe. Additionally, it introduced the Eagle Corr PE, a product used in a variety of gravity flow applications and is ideal for storm sewer systems. Eagle Corr PE has a high strength-to-weight ratio, is very flexible and weighs much less than traditional products, making it easier to install without sacrificing durability or structural strength.
“We’re used to doing a lot of loading and locking up of pipe. There’s a whole lot of difference using the JM Eagle product,” says Steve Mitchell, production pipe foreman for Dallas 1 Construction & Development, who install pipe on a daily basis. “There are virtually no man-hours needed for the restraints. Personally,
I think the [Eagle Loc 900] system is fantastic.”
“We are excited about 2010,” concludes Slawson. “We are going to be offering even more new products and introducing programs that will allow us to better serve our customers.”